Sealed for Safety: Pantnagar’s 72‑Hour Antibacterial Plastic Marks New Era in Hygiene
Scientists at GB Pant University, Pantnagar, have developed an antibacterial plastic that resists microbial contamination for 72 hours. This article explores the materials science behind it, how contamination is prevented, and the regulatory path toward widespread adoption in food handling and healthcare.
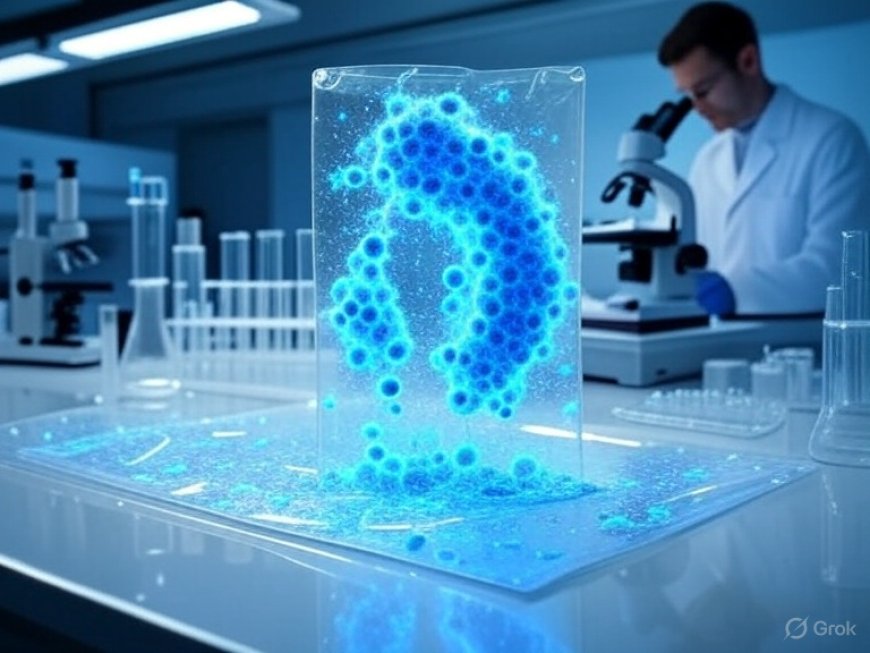
1. A Fresh Frontier in Material Safety
On July 11, researchers at GB Pant University of Agriculture & Technology (GBPUAT) in Pantnagar unveiled an innovative antibacterial plastic capable of resisting microbial contamination for up to 72 hours, even when exposed to air and water The Times of IndiaCabinet Digital Library+1The Times of India+1Govind Ballabh Pant University+1The Times of India+1. The development signals a potential game-changer for sectors like food packaging, healthcare, and consumer plastics, where contamination is a pressing concern.
2. The Science of Surface Protection
This new plastic integrates antibacterial agents into the polymer matrix, creating an environment hostile to microbes like E. coli, Staphylococcus aureus, and Salmonella. By releasing these agents in controlled amounts when in contact with moisture, the surface remains inhospitable to microbial survival or growth over three days. This builds on proven antimicrobial-film technologies used in food science .
3. Why 72 Hours Matters
Research shows most microbial contamination becomes unsafe within 24 to 48 hours. Extending resistance to 72 hours offers a critical buffer. For consumers, it means safer handling; for health providers, it reduces infection risks associated with plastic touchpoints. Additionally, in food transit—where packaging may be reused or stored—the plastic could delay spoilage and reduce food waste.
4. Potential Applications
-
Food packaging: Refrigerated and ambient applications where bacterial growth threatens shelf life and safety.
-
Single-use medical gear: Bandages, sample containers, catheter tubing—fields where contamination poses serious risk.
-
Everyday items: Reusable bottles, cutlery, mobile covers—especially useful during epidemics or in hygiene-conscious markets.
Each of these uses depends on proof of efficacy, safety, and durability under real-world conditions.
5. The Manufacturing Process
Incorporating antibacterial agents demands precise technique. The plastic polymers undergo compounding at specific temperatures to evenly distribute agents without impairing material integrity. This ensures longer-term efficacy while maintaining essential mechanical properties—like tensile strength and flexibility—that standard plastics offer.
6. Meeting Regulatory Milestones
To shift from lab to market, the antimicrobial plastic must satisfy multiple regulatory standards:
-
Safety certification – Confirming additives are non-toxic and safe for food contact.
-
Efficacy validation – Under ISO 22196 / ASTM E2180 standards, confirming 72-hour antimicrobial performance.
-
Environmental compliance – Ensuring recyclability or biodegradability, critical under proposed plastic waste regulations.
-
Scale-up consistency – Protecting agent distribution and performance across industrial batches.
GBPUAT’s partnerships with the Bureau of Indian Standards (BIS) and the Food Safety and Standards Authority of India (FSSAI) will be vital to secure real-world deployment.
7. Challenges to Commercial Roll-out
While promising, the technology faces barriers:
-
Cost implications: Added antimicrobial agents and specialized processing may increase production costs. Adoption will require clear ROI—such as reduced spoilage costs or healthcare savings.
-
Additive longevity: The antimicrobial effect must not degrade rapidly over time or after exposure to heat, UV rays, or cleaning chemicals.
-
Consumer acceptance: Public confidence is essential. Transparent labeling, independent testing, and clarity about the plastic’s longevity and safety will be essential.
8. Materials Science and Innovation
The breakthrough draws on a lineage of antimicrobial research including:
-
Cellulose-based anti-infective films, effective against E. coli and S. aureus within minutes .
-
Nanoparticle-enhanced biofilms, such as silver-embedded starch coatings for food packaging, offering both microbial resistance and biodegradability The Times of India+2arxiv.org+2arxiv.org+2.
Pantnagar’s innovation uniquely merges industrial durability with sustained antibacterial performance—paving the way for real-world use.
9. Voices from the Laboratory
“We tested common bacteria under simulated-use conditions—wet, dry, varied temperature—and maintained no detectable contamination for at least 72 hours,” said a lead researcher at GBPUAT’s polymer science wing The Times of IndiaGovind Ballabh Pant University.
“The next challenge is replicating these findings at scale—industrial molding, packaging trials, lifecycle analysis,” the team added, acknowledging the road ahead from prototype to product.
10. Connecting Hygiene to Climate Goals
As sustainability becomes central to product design, antimicrobial plastics must align with circular economy principles. Pantnagar's team is exploring biodegradable additives and recyclable polymers to ensure environmental compatibility—supporting goals like India’s Plastic Waste Management rules.
Integrating antimicrobial features and eco-friendliness places this innovation within a broader sustainable materials science ecosystem.
11. Global and Domestic Positioning
Internationally, companies are racing to embed antibacterial traits in household products, but India's domestic research capacity is limited. Pantnagar’s initiative positions India alongside global leaders in advanced packaging technologies. If scaled successfully, Indian-made antimicrobial polymers could serve local needs—such as rural healthcare—and reduce import dependence.
12. Building an Innovation Ecosystem
This milestone highlights the vital relationship between academic innovation and industry uptake. GBPUAT’s roadmap must include:
-
Partnerships with polymers and packaging firms
-
Joint lab-to-market initiatives with Indian biotechnology startups
-
Technology licensing models with clear IP terms but affordable access
These steps will ensure the antibacterial plastic moves beyond academic prominence into marketable application.
13. Towards Consumer Trust and Safety
Effective branding and labeling will be crucial. Consumers must see clear claims—such as "72‑Hour Antimicrobial Protection"—backed by:
-
Third-party lab validation
-
Regulatory certifications
-
Testimonials from sectors like food processing or hospitals
Public education about antibacterial plastics and their role in hygiene will build confidence.
14. Looking Forward: The Road Ahead
Pantnagar’s print is a significant milestone—but next steps will test its viability:
-
Pilot batches with manufacturers
-
Field studies in real conditions (packing, shipping, storage)
-
Life-cycle environmental assessments
-
Regulatory clearances from FSSAI, CDSCO, BIS
-
Market trials targeting hospitals or food packaging companies
Success in these phases could open the door to nation-wide adoption and potential export.
15. Conclusion: From Lab Discovery to Everyday Safety
Pantnagar’s antibacterial plastic is more than a lab innovation—it’s a glimpse at a future where every plastic surface can help prevent microbial spread. The next few months will determine whether this becomes a mainstream material in India’s drive toward safer food, cleaner hospitals, and sustainable products.
This innovation is significant—and if delivery meets promise, it could redefine how a nation engages with everyday hygiene through material science.